Customer:
One of world’s reputed manufacturers of turbochargers and turbocharger components. Our customer is a trusted Tier-I supplier of turbochargers to automotive and industrial domains.
Business Challenge:
A turbocharged engine is very important to leverage the benefits of:
- Lower emissions.
- Lower fuel consumption.
- Lower engine noise.
- Enhanced engine power, torque and more.
Within the turbocharger, the turbine shaft connected to the compressor supplies the compressed air to the engine for efficient fuel burning.The position of the vane dictates the amount of air that can be compressed and hence significantly influences the overall efficiency of the turbocharger.
Our customer had designed a product roadmap for the next generation turbocharger with Electronic Smart Actuator (ECA), a closed loop system that will electronically control the position of the vanes based on the inputs from engine ECU (or control unit) and CAN/LIN interface. Development of such an ECU hardware and software would ensure improved efficiency of the next-gen smart turbocharger.
Our customer was looking for a Product Engineering Services partner with expertise in ECU (Electronic Control Unit) software and hardware development.
Embitel Solution:
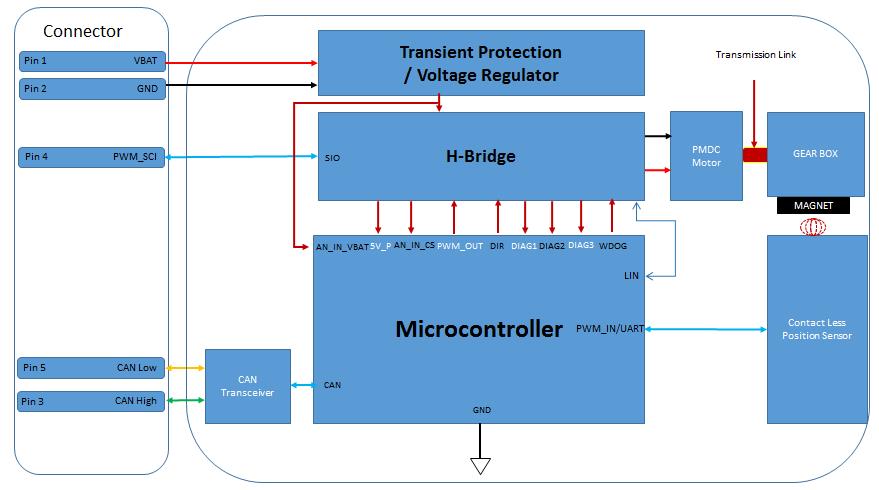
Smart Actuator ECU (Electronic Control Unit) software development:
- Our automotive embedded software development team proposed a layered architecture for the actuator ECU software of engine turbocharger.
- This layered architecture of the ECU (control unit) software had the benefits of ease of software testing and maintenance. Following are the details:
-
- Target Abstraction Layer (TAL):Our embedded software development team designed low level drivers on RL78-F13 Microcontroller platform for MCU, ADC, PWMIN,PWMOUT,LIN,CAN and UART interfaces.
- Hardware Abstraction Layer (HAL):We designed a reusable, configurable and hardware-independent firmware.
This Hardware Abstraction Layer ensures that the ECU software application developer has a set of standard functions that can be used to access hardware functions without detailed understanding or dependence on the underlying hardware platform.
HAL firmware also ensures ease of migration to a different upgraded hardware platform without any changes in automotive ECU software code.- Data Abstraction Layer (DAL): The Data Abstraction Layer was designed to convert raw data from the CAN/LIN or other vehicle interface into a physical value and send it to the ECU software application layer (e.g physical value of Battery Voltage instead of ADC raw data).
-
- We partnered with the Tier-I Supplier for design and development of Base software modules and Signal Layer software drivers for the actuator ECU.
- The ECU software development process was compliant withV-Cycle SDLC model (SWRS , HLD , LLD , MTD , >90 % Unit Test Coverage).
- ECU Software drivers were designed and developed for ADC, PWM IN/ PWM OUT, CAN/LIN and UART along with Magnetic Sensor Interfaces.
- Our automotive software developers also designed a Scheduler for the actuator ECU (electronic control unit).
Actuator ECU (control unit) hardware development:
- Our automotive Control Units (ECU) hardware development team partnered with the tier-I supplier for end-to-end ECU hardware development.
- Following are the details of the ECU hardware development process:
- Hardware Requirement Specification document was designed for the actuator ECU.
- Circuit Design and simulation of each component.
- Layout design.
- E-BOM procurement.
- Fabrication.
- ECU Hardware Assembly.
- Board bring-up.
- Functional Testing of the developed ECU hardware.
- The entire ECU hardware development was complaint with the automotive grade and safety standards.
- A detailed compliance testing was done for the ECU hardware through EM Analysis and Thermal Analysis.
Tools and Technologies:
- Renesas RL78/F-13 Family Microcontroller.
- IAR Embedded Workbench.
- ORCAD: Schematic Design.
- Allegro: Layout.
- Hyperlynx 8.0 : EM and Thermal Analysis.