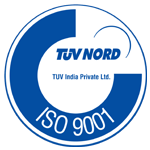
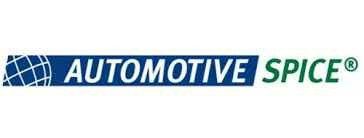
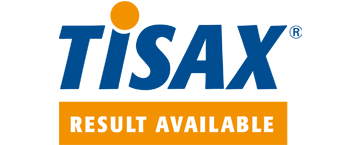
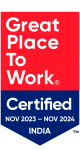
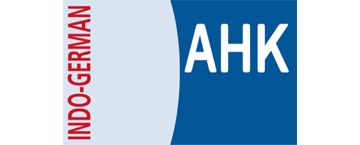
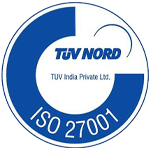
Configuration and Integration Services for Automotive Application Development Projects
FlexRay protocol stack is emerging as the COM stack of choice for safety critical automotive applications such as ADAS, Body Control Module, Battery Management Systems for EVs and more. FlexRay is capable of offering higher data transfer rate to the tune of 10 Mbit/second.
Features such as full determinism and composability make FlexRay the ideal communication stack to enable real-time, fault tolerant communication in modern automotive applications.
Business Model for our FlexRay IP
Our FlexRay Protocol Stack (ISO 10681-1:2010) is a pre-tested software solution, designed keeping in mind your automotive product development projects. This industry recognized FlexRay protocol solution is offered under a one-time licensing fee model.
Under this business model, as a customer, you are the joint owner of the IP rights of the software as well as the source code of the FlexRay protocol stack. This makes you entitled to deploy and integrate the FlexRay protocol stack across multiple series productions.
Configuration and Integration Services for Automotive Application Development Projects
Our FlexRay stack has been designed to power modern automotive applications including:
- Body Control Module
- Battery Management System
- Advanced Driver Assistance System
- Electronic Power Steering
- Antilock Braking System
Software Stack for FlexRay Protocol (ISO 10681-1:2010): Details of the Software Architecture
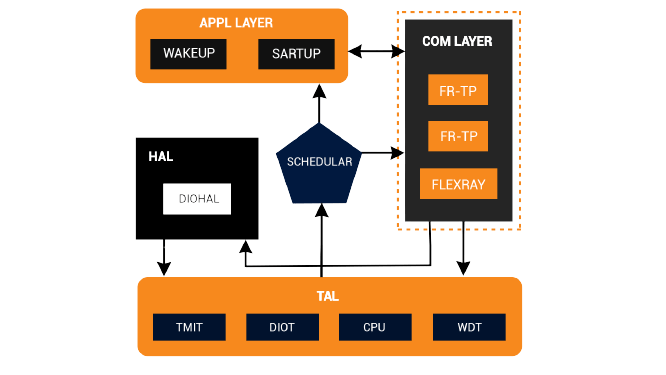
200+
customers supported since 2010
100+
scalable and reusable Bootloader platforms delivered
30%
quicker time-to-market enabled
95%
lesser development time with PC-based automation tools
FlexRay Software Stack Comprises of the Following Layers and Software Components:
FlexRay drivers enable access to the hardware resources for the upper software layers. The drivers are developed based on the Microcontroller platform used in the project. For example, it allows FlexRay IF layer to access FlexRay transceiver and FlexRay communication controller.l
The transport layer is the hardware independent layer and is used for segmentation and reassembly of the messages that do not fit into one data frame which is 254 bytes in size.
The role of the FlexRay IF layer is to provide a specified interface to the com system for the upper layer modules like application layer. However, this role is limited only to the flow of data.
Factsheet for FlexRay Protocol Software Specifications and Features
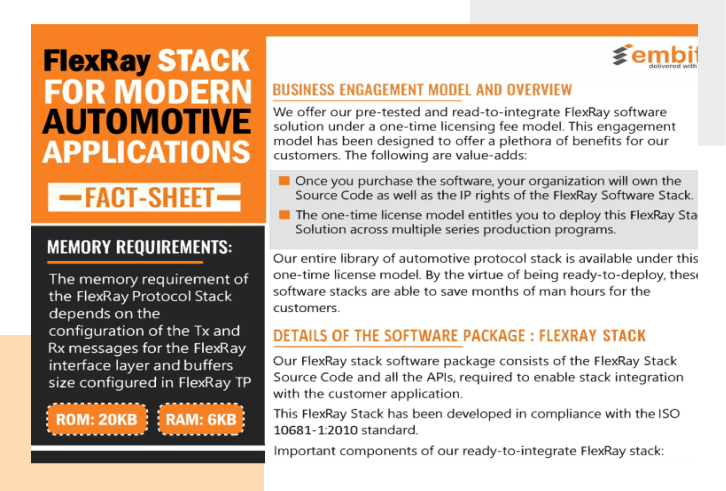
This downloadable Fact sheet contains all the details of our production-grade and ready-to-integrate FlexRay protocol stack. This (ISO 10681-1:2010) compliant software is popularly deployed for modern automotive ECUs to support applications that require faster data transfer rates and higher data payload value.
Download this FlexRay factsheet to get following information:
- Our FlexRay stack engagement model, and overview
- Benefits of IP rights and FlexRay source code
- FlexRay solution package, features, memory requirements and use cases
- FlexRay protocol software integration, maintenance, and support services
Please refer to FlexRay stack FAQ’s for more details.
FlexRay Protocol Stack Configuration, Integration and Testing Services
Development and Integration of FlexRay Device Drivers
- Readily available drivers for Renesas – RH850 and NXP 5748G
- Support will be provided to develop the FlexRay drivers for customer specific microcontroller
- Configurable Hardware Filtering mechanism
- Configurable Message buffers
- Support for FlexRay device driver integration, across production programs
Development and Configuration of FlexRay Interface Layer
- Ready-to-deploy FlexRay Interface layer (FR IF); only configuration is required
- Tx and Rx message configuration from the FIBEX file
- Support for configuration of FlexRay Interface layer
- Configurable Skeleton code for FlexRay Interface layer is also available
- Low level and high level documents are provided
- Support for software level message filtering
- Signal and message extraction provided as a default feature
FlexRay Protocol Stack Support and Maintenance Services
- Creation of High Level Design documents (HLDD) and Low-Level Documents (LLD)
- Integration and Functional Testing support using Vector FlexRay tool
- Support for MISRA compliance report creation
- Unit Testing support using Tools like Tessy
Integration and Configuration of FlexRay Transport Layer
- Integration and configuration of FlexRay TP Layer
- FlexRay TP implementation as per IS0 10681-2
- TP module handles both Segmented and Unsegmented messages
- Built-in error handling feature
- Ready-to-deploy TP layer for reduced turnaround time
Value-Adds of FlexRay Stack over CAN Bus Protocol Stack
Controller Access Network (CAN) | FlexRay |
---|---|
Supports a max data rate of 1 Mbps | Supports data rate of 10 Mbps |
Supports only asynchronous message transmission | Supports both asynchronous and synchronous message transmission |
Its usage is based on soft real time | Fulfills hard real-time requirements of applications |
CAN is a single-channel bus; no redundancy | FlexRay is dual-channel; thus, brings in built-in redundancy in the network |
Lack of composability; nodes added or removed from the network have an impact on the scheduling | FlexRay has high composability and is dynamic; nodes can be tested externally and added to the system easily |
CAN frames support only 8 bytes of data field | FlexRay frames support a data field containing up to 254 bytes |
Customer FAQs Related to FlexRay Stack Development and Integration
Ans. The modern automotive applications stipulate transmission of larger amounts of data at optimum rates across the vehicle network. However, CAN BUS protocol supports the transfer of only up to 8 bytes of data.
FlexRay has emerged as the choice communication protocol for such applications.
Following are the business use-cases of our FlexRay stack:
- Telematics
- Powertrain Electric Vehicle powertrain
- Body Control Module
- Infotainment System
- Battery Management System
Ans. FlexRay driver is the only part of the stack that is dependent on the hardware platform. Rest of the software layers, like FlexRay Interface and FlexRay Transport layers are hardware agnostic.
This implies that the FlexRay driver will need to be developed based on the microcontroller used in the project.
Our automotive team has expertise of developing device drivers for all major MCU families including Renesas, NXP, Fujitsu, TI and others.
Ans. Yes. Our service level agreement for FlexRay Protocol Stack clearly documents the fact that we will provide all the necessary configuration and integration services, along with CAN protocol stack license.
Tool-level integration for low-level drivers as well as application level, will also be a part of our SLA.
Ans. Our pre-tested FlexRay stack solution consists of the following software services. The low level device drivers are platform dependent.
- FLEXRAY Device Drivers
- FLEXRAY Transport layer
- FLEXRAY Interface Layer
Ans. According to our existing business model we provide one-time licensing to our customer. This includes IP rights and source code of the FlexRay protocol software. This model benefits the customer, as it lends flexibility of integrating the software stack across multiple projects or product lines.
However, our business model may be re-planned according to the customer’s needs.