Complexity of modern automotive software demands development methodologies that save time and ensure reliability. We at Embitel, achieve this by using Model Based Design(MBD) powered by tools like MATLAB, Simulink and Simscape, and more.
Automation of Model Based Design processes like code generation, testing and documentation lead to faster time to market something that automotive companies always aspire. Model Based Development (MBD) can result in average costs savings of 25%-30% and time savings of 35%-40% (according to a global study by Altran Technologies, the chair of software and systems engineering and the chair of Information Management of the University of Technology in Munich)
Over the past decade, our team of MATLAB programming experts has been delivering cost and time savings with Model Based Design approach for product development.
Use Cases for Model Based Development of Automotive Embedded Software
Embitel has successfully delivered automotive software developed using Model based design methodology. Our expertise in MBD powered automotive product development spans across the following areas:
MBD Software Code Generation: Compliant with Automotive Industry Standards
AUTOSAR compliant MBD code generation, with the help of tool-boxes like E-coder, AUTOSAR ERTL etc.
Complete conformance to Mathworks Automotive Advisory Board (MAAB) guidelines in module development using Model Advisor toolbox
Deployment of tools like Polyspace to ensure that the software code generated using the Model Based Design approach is MISRA C compliant
A Handbook on Model Based Design
Download PDF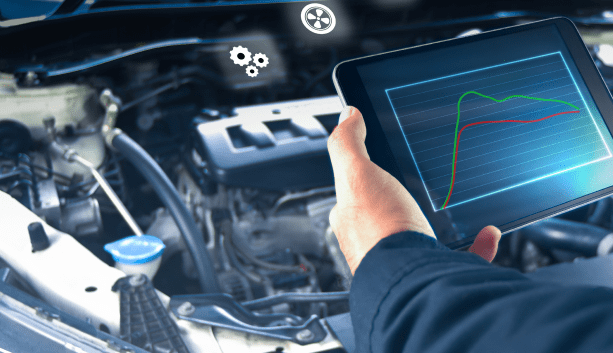
Model Based Design Services for Automotive Product Development
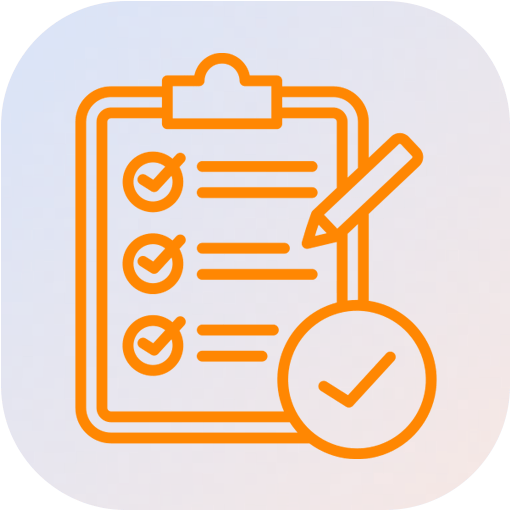
Requirement Maturation
- Model Based Design of System level architecture and solution services
- Identification of maximum possible issues/queries during H/W & S/W requirement analysis
- Requirement freezing after resolution of these issues
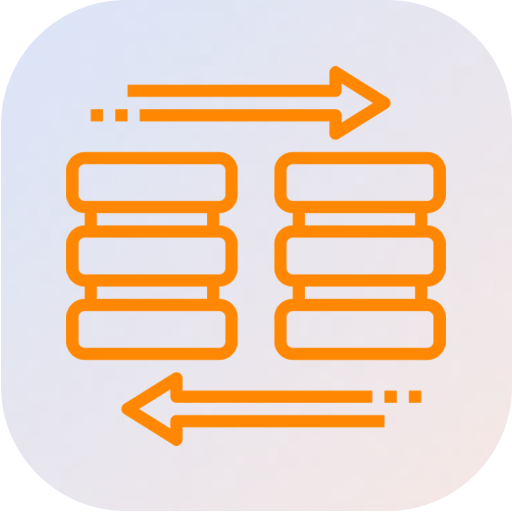
Migration from Non-MBD to MBD paradigm
- Architecture Development mapped with Model Based Design paradigm
- Modules/ Component Development in MATLAB, Simulink, Stateflow as per MAAB guidelines
- Memory Optimization for RAM/ROM according to MAAB guidelines
- ISO 26262 Compliant Models Rapid Prototyping- Virtual Prototyping, External Bypass etc.
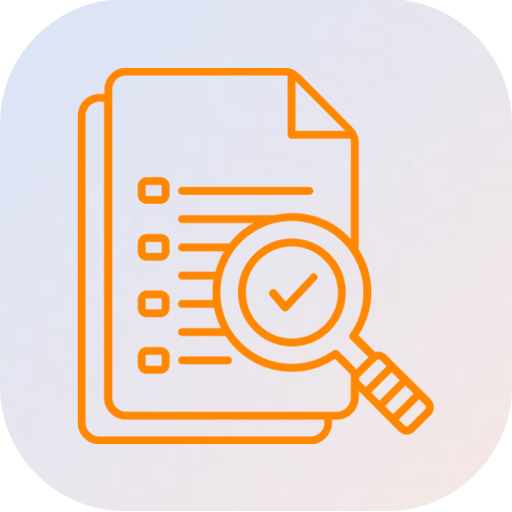
Verification & Validation Services
- Model in Loop Testing (MIL)
- Software in Loop Testing (SIL)
- Hardware in Loop Testing (HIL)
- Processor in loop testing (PIL)
- Simulink Design Verifier
- Verification and Validation (V&V) of MATLAB Simulink Models
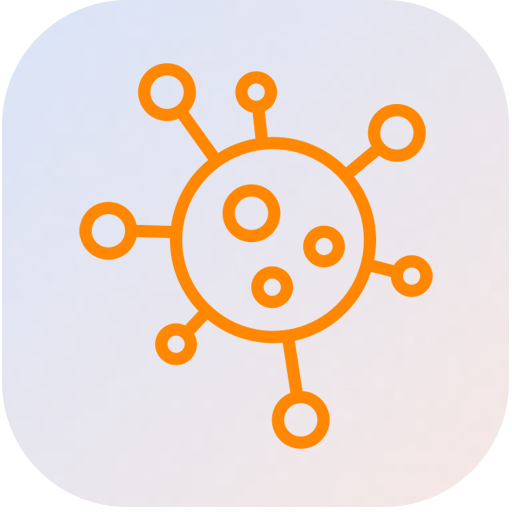
ISO 26262 Compliant MBD approach
- Software development in compliance with ISO 26262 (part 6)
- Support for development focused on ISO 26262 requirements specific to Model Based Design
- All additional V&V requirements are fulfilled based on ISO 26262 standard
- Models are created based on the requirements as per the ISO 26262 Model Based Design guidelines
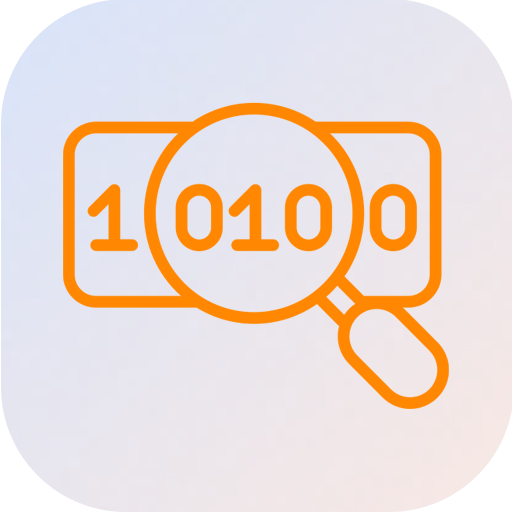
Auto Code Generation
- Code Generation using Target Link (MATLAB model conversion to Target Link Model)
- Code Generation with Matlab E-coder
- MISRA, AUTOSAR compliant code
- Custom Code Generation with Custom Target Language Compiler and E-coder
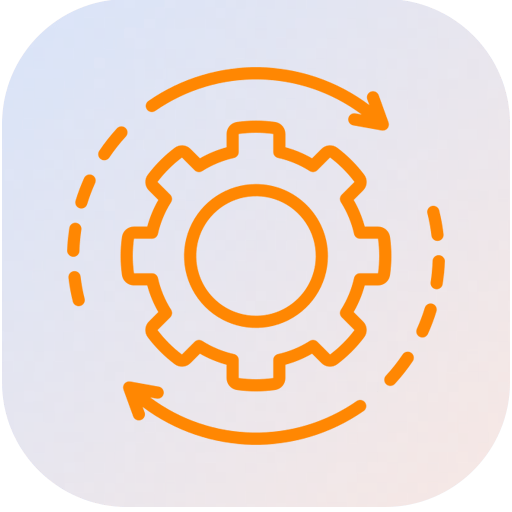
Integration Services
- Application & LLD Interface Development
- Integration Testing in real time environment to ensure error free module interactions
- Testing on real-time hardware (bench testing) (HIL)
- Testing on a target processor if real-time hardware is not present (PIL)
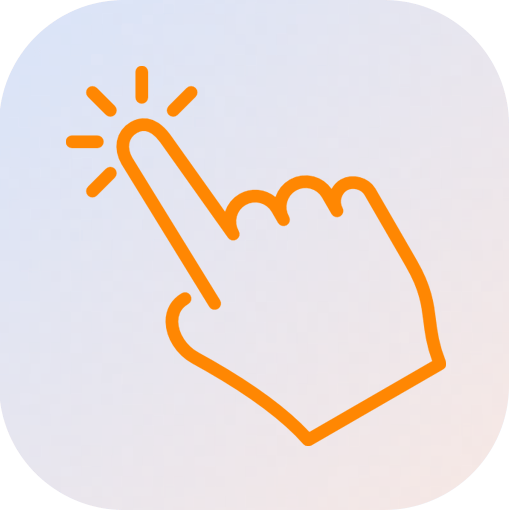
Floating to Fixed Point Conversion
- Support for Conversion of Floating point models to Fixed point models as per customer requirements using Mathwork Fixed Point Converter Tool Box.
- Support for Conversion of floating point Matlab code to fixed point code.
- Code generation & testing of floating and fixed point models for the comparison of results, in order to ensure expected accuracy.
Video Explaining How Model Based Development Works?
Customer Success Stories of Model Based Design and Development
Our Expertise inModel Based Design Tools and Technologies
- Target Link for MIL Testing and SIL Testing
- E-coder for code generation
- GT-Power, Amesis, Tess for Environment Model Development
- ASCET, Statemate and SCADE for functional development
- AUTOSAR ERTL (for AUTOSAR compliant code)
- Custom Target Language Compiler (for customized compilation)
- Vector tools for Hardware in Loop (HIL) Testing
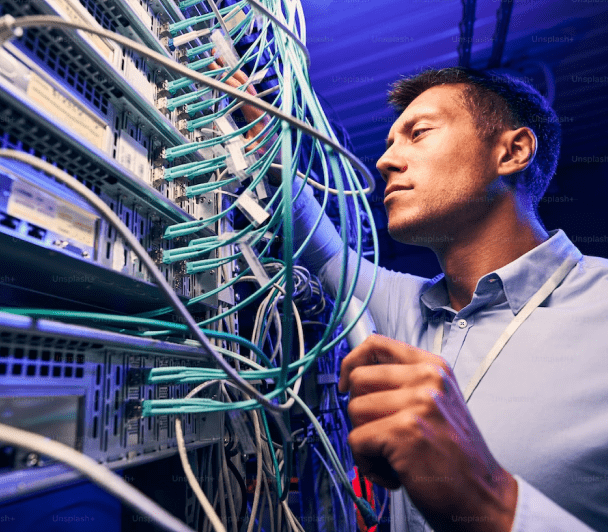
Embitel’s Model Based Development Methodology
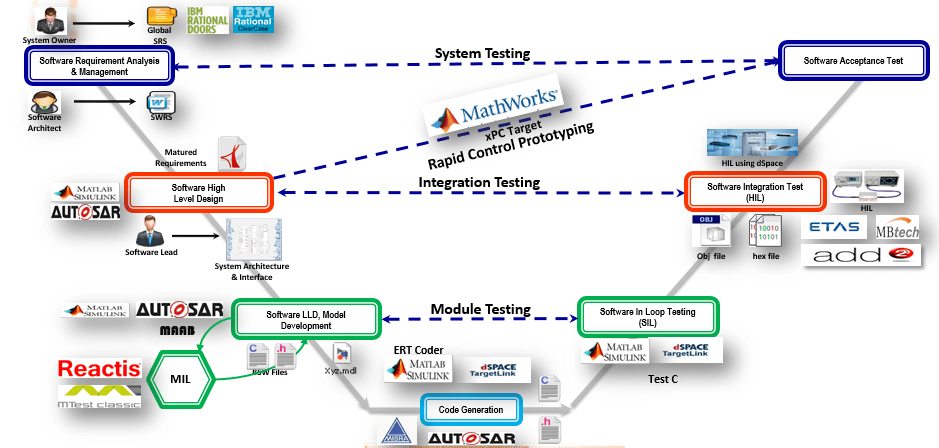
FAQ’s Regarding Model Based Design
- More accurate conversion, better quality of the code and very less turn-around time.
- Support for Documentation related to each and every phase of V based SDLC model.
- ISO 26262 compliance
- AUTOSAR based model development
- Test plan, test cases creation
- I/O documentation for every phase of V-cycle as an evidence for CMMI or other QA audits
- Veteran Model Based Development Managers, who ensure end to end V cycle based MBD project execution. Compliance to the organizational process execution model is also ensured by them to the highest level possible.
- Senior MBD Consultants with 14+years of experience, to partner with you for critical automotive projects for product (ECU)/application development and consulting support.
- Senior MATLAB programming experts proficient in developing automotive ECUs/applications as per the latest industry standards including MAAB, AUTOSAR, and ISO 26262.
- Getting ready for the migration: Includes assessment of current state of the development process and learning the core MBD tools.
- Feature selection as per project scope: Understanding and fin-tuning of scope and requirements at every phase of development, selection of features, modeling and simulation and code generation.
- Component selection and physical modelling: Activities include Expand modelling, simulation at component level and introduction of plant modelling.
- Standardization: Performing Simulation at system level and full model based verification and validation. Best practices like introduction of tool automation and creation of reusable libraries also come into picture.
- Optimization: The final phase is to align the MBD approach with enterprise vision and goals. Objective is to make the processes fully automated and optimized.
Ans. Model-Based Design (MBD) in the automotive software landscape facilitates the design, simulation, and testing of automotive software before physical prototypes are built.
Related Blogs & Webinar: Learn More About Model Based Design
- [Video] How a Transition to Model Based Development can Save your Product Engineering Teams from Manual Coding Syndrome
- Why the Transition from Code Based Development to Model Based Development is a Necessary Paradigm Shift in Automotive
- [Video Blog] How Model Based Development Works: A Step-by-Step Analysis
- [Webinar] Model Based Development Tutorial: How to Create Models using MATLAB/SIMULINK
- [Webinar] Model Based Development Tutorial: How to generate code from the models using MATLAB/SIMULINK
Knowledge bytes
• Why choose Model Based Design Over Manual Coding?
- Reduced system complexity
- Test suite reusability
- Design reusability to multiple hardware target deployment
- Automatic code generation
- Continuous error identification and correction
- Enhanced efficiency of up to 50%
- Reduced time-to-market and overall cost of development
Model Based Design
- 1. Model Based Design (MBD) is a software development methodology based on V-cycle.
- The model based approach enables a developer to simulate the models for the complex control processes.
- These software models can be tested to assess the performance in real-time. Once finalized, the code can be auto-generated from the models, using code generation tools.
- This way, the product can be tested at every stage of its development before the code is generated.
Here is a snapshot of Model Based development process:
- Requirement Maturation: Hardware and Software requirement analysis is performed as the first step to weed out maximum number of design issues.
- Model Simulation: The desired functionalities are expressed in the form of mathematical formula which eventually become models using simulation tools like MathWorks Simulink.
- Testing and Validation: Software-in-loop, model-in-loop and hardware-in-loop testing are performed on the model. As it is an iterative cycle, any issue found at any stage is rectified by tracing it back to its previous stage.
- Code Generation: Code is auto generated from the tested and verified models.
What are the Benefits of MBD?
- The advantages are many that have made model-driven approach, a method of choice for automotive software development. Model Based Design approach renders a great value-add for development of powertrain and chassis control applications, in particular.
A few of MBD’s advantages:
- Continuous testing of the software at every stage ensures that it is free from bugs/ errors and is of the highest quality.
- Time-to-market is reduced considerably as code doesn’t have to be written manually.
- MBD makes it easier to design Complex functions, as it requires less iterations.
- Cost of development is reduced.
- Test suites can be reused for different production programs.