Vehicle diagnostics as a process has undergone numerous transformations over the past 2 decades. The demand for a more accurate, standard and efficient fault detection in vehicle diagnostics, has led to breakthrough innovations and developments.
Evolution of Vehicle Diagnostics:
Earlier, there were flash codes wherein technicians had to look for flashes and convert them to codes or sometimes the technician had to physically remove vehicle components, disconnect wires for fault detection.
The increasing complexity of vehicle systems over the time mandated the need for diagnostics standards to efficiently track their scope and relevance.
To cater to this need of the hour, various vehicle diagnostic protocols were conceptualized and developed.
ISO and SAE (Society of Automotive Engineers) introduced various diagnostic protocols and standards, designed to cater to the different types of automotive ECU systems and diagnostics specifications from the vehicle manufacturers.
OBD II (On-Board Diagnostics), K-Line per ISO 9141-2, KWP 2000 (Keyword Protocol 2000), UDS (Unified Diagnostic Services) are some of the vehicle diagnostic protocols designed and deployed during the evolution in off-board and on-board vehicle diagnostics.
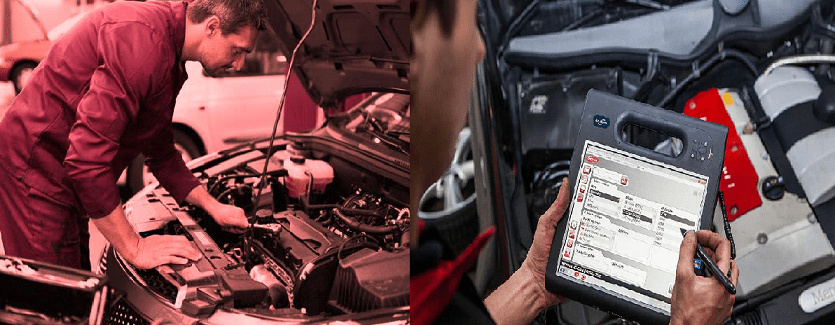
Image credit: nextews.com & brezan.nl)
Although a large number diagnostics protocols and  systems were developed and used within the automotive industry, many of them have become obsolete due to the rapid “Electronification “of the automotive ECU (control units).
As of now, Keyword Protocol 2000 (KWP 2000) and Unified Diagnostic Services (UDS) remain one of the most widely used vehicle diagnostics protocols. Let us have a look at two protocols in detail:
KWP 2000:
KWP2000 or the Keyword Protocol 2000 is an on-board diagnosis (OBD) protocol complaint with ISO 14230 standard.
It defines a common set of communication codes, for exchange of data, used by vehicle ECUs as per the guidelines the OBDII regulatory standard. KWP 2000 is compatible with both K-Line (ISO 9141) and CAN (ISO 11898) in-vehicle networking systems.
The KWP 2000 protocol uses a physical layer, identical to ISO 9141-2, for bidirectional serial communication over K-line with the controller. The protocol also uses L-Line (optional) unidirectional communication, to wake up the automotive ECU.
The average data rate of KWP 2000 is between 1.2 and 10.4 kilo baud, and the data fields within the message may contain up to 255 bytes.
UDS protocol – Unified Diagnostics Service:
The Unified Diagnostics Services protocol (ISO 14229) is an off-board diagnostic system. It is designed in compliance with ISO 14230-3 (KWP2000) and ISO 15765-3 (Diagnostic Communication over Controller Area Network (DoCAN)) standards.
The maximum size of message supported within UDS is up to 8 bytes. For exchanging messages exceeding 8-bytes, the UDS protocol uses ISO 15765-2 layer, an international standard for transfer of data packets over a CANBus. UDS diagnostic implementation is independent of the underlying physical layer and is also compatible over both LIN and CAN in-vehicle networks.
UDS as a diagnostic protocol was developed to unify all the diagnostics standards that existed previously and to come up with a single valid set of diagnostic services for the automotive ECUs.
This has ensured that integration of the UDS protocol stack reduces the additional costs for the development of diagnostic communication applications.
Comparison Between KWP 2000 and UDS Protocol:
While, UDS protocol can be seen as a superset of the KWP 2000, since it is derived from the latter, a comparison of both as the diagnostic protocols gives out some interesting facts:
- Support for in-vehicle communication networks: The KWP 2000 protocol supports CAN and K-line bus systems . The UDS protocol is designed to be independent of the underlying vehicle network as it supports a range of bus systems including CAN, CAN -FD, LIN, etc.
KWP 2000 is highly preferred where the vehicles are based on legacy systems such as K-line. Otherwise, these days UDS protocol is the go to standard for vehicle diagnostics.
- Transfer of Key Measurement Values: Both the diagnostic protocol facilitate exchange of request and command messages from the test equipment to the automotive ECU; and key measurement values (data) in response from the vehicle ECU.
But, there is a key difference between the two protocols in the way these measurement values are exchanged between the tester and ECU:
UDS uses the 2-byte dataIdentifiers (DID), whereas the KWP uses a 1-byte recordLocalIdentifier and 2-byte commonIdentifier.
The advantage of the UDS protocol is that the tester can request several measurement values with one UDS service request using its 2 bytes ( 16 bits) long data identifiers as compared to the 1-byte ( 8 bits)Â Local identifier used by KWP 2000 standard. This means increased efficiency of data exchange. - Diagnostic Communication between Test equipment and vehicle ECU: The exchange of messages between testing device and the vehicle ECU forms the basis of the diagnostic system.
The natures of request and response messages and data transfer interval between them form an important factor in vehicle diagnostics.
KWP2000 favors symmetrical communication sequence where the number of request and response messages between the testing device and server are symmetrical.On the other hand, UDS is based on an event driven and periodic communication sequence. This means, the number of request and response messages can be different.
Moreover, in a periodic communication sequence based on UDS standard, the test equipment sends periodic requests for updated information from automotive ECUs. This helps in closely monitoring vehicle condition in regular intervals. The vehicle ECU may respond to the periodic request with one or several data record values.This also helps in identifying any deviation from the threshold/ideal values associated with crucial vehicle functions such as airbag deployment , engine fuel injection, engine speed and heating etc.
Thus UDS offers more detailed information related to the fault through periodic update. - Error Memory Management: While the KWP 2000 provides 4 services for error memory management, the UDS protocol specifies just two services.
KWP 2000 uses following services for error memory management:
$14 (clearDiagnosticInformation),
$18 (readDTCByStatus),
$17 (readStatusOfDTC), and
$12 (readFreezeFrameData).While, UDS uses only the
$14 (clearDiagnosticInformation) and
$19 (readDTCInformation)With the help of the readDTCInformation service in the UDS protocol , the testing device can not only read diagnostic related DTC data, but it can also read additional parameters of the component ( say engine)Â at the time of the occurrence of fault. This helps in pinpointing the root cause of fault/damage and then undertaking the right repair and maintenance operations.
- Read DTC Subfunctions: The KWP2000 protocol specifies 3 function for the Read DTC ( Read DiagnosticTroubleCodes) service . On the contrary, the UDS protocol specifies 21 sub functions for the Read DTC service.
With the help of the additional sub functions, UDS enables the tester to collect more diagnostic information. This is useful in the modern automotive industry where the complexity of design and number of components in the vehicle are increasing.
KWP and UDS- A Quick Comparison:
Parameters | KWP2000 | UDS |
ISO Standard Compliance | Is based on ISO 14230 | Is based on ISO 14229-1 and is derived from ISO 14230-3 (KWP2000) and ISO 15765-3. |
Protocol Dependency | KWP 2000 functionalities for measurement value transfer and error memory management were improved for UDS standards. | It is an extended version of KWP2000 on CAN (specified under ISO 15765-2) and many other previous diagnostic standards. |
Tester-ECU Communication: | Supports a symmetrical number of requests and response between the tester and the ECU(s). | Is based on event-driven and periodic services. Hence number of requests and response between the tester and the ECU can vary. |
Transfer of measurement values: | Involves a 1-byte “record Local Identiferâ€Â and another 2-byte  “Common Identifer†| Involves 2-byte data identifier and allows higher number of IDS to be exchanged. |
Error Memory Management: | Specifies four services for the error memory management: $14 (clearDiagnosticInformation), $18 (readDTCByStatus), $17 (readStatusOfDTC), and $12 (readFreezeFrameData). |
Specifies two services for error memory management: $14 (clearDiagnosticInformation) and $19 (readDTCInformation) |
Read DTC Functions | KWP2000 specifies 3 subfunctions under the ReadDTC service | UDS specifies 21 sub functions under the ReadDTC service |
Vehicle Network Supported | Runs on several transport layers such as K-line (serial) or CAN. | It is independent of the vehicle bus systems. Runs on CAN, LIN, and Ethernet on transport protocol. |
ECU Identification | Contains a specific function to identify the ECUs – Read ECUIdentification | Doesn’t include a separate service to identify the ECU, rather this functionality is included within the Read databyidentifier. |
Reference: Road Vehicles: Diagnostic Communication : Technology and Applications- By Christoph Marscholik, Peter Subke
KWP 2000 and UDS are both used in modern automobiles for efficient and accurate diagnosis of vehicle health and faults. Over the time, UDS protocol owing to its robustness and a broader service spectrum is expected to be the future of automobile diagnostics.
UDS protocol is defined by redundancy of functionalities whereby various UDS services can be used to execute a certain diagnostic function. For example, both SIDs 0x36 (TransferData) and 0x3D ( writeMemoryByAddress) are effective for flash memory programming. Similarly, any of the 0x2E (writeDataByIdentifier) and 0x3D (writeMemoryByAddress) can be used for data manipulation within ECU.
Thus, UDS as a diagnostic protocol paves way for added services and functionalities. But it also calls for additional requirement for ECU memory along with extra development costs. Thus it is important to ponder over certain questions, before deciding on the implementation of UDS services for your application, listed as:
- What services are necessary for you?
- What sub functions and parameters are important to be considered for UDS implementations?
- What data identifier and parameters should be focused on?
If you take these questions into account, you will be able to successfully implement UDS within your automotive application without any unnecessary development costs or efforts. Talk to our Automotive experts to know how you can seamlessly implement and integrate UDS software stack according to your automotive use-case.