About the Customer:
Our customer is a leading automotive tier-1 supplier with a focus on delivering cutting-edge solutions for air quality improvement in vehicles. With a commitment to sustainability and passenger well-being, the customer plays a crucial role in enhancing the in-cabin experience for automotive manufacturers worldwide.
Business Challenges:
The customer had successfully designed and manufactured all the mechanical components required to build an advanced in-cabin air purification system.
However, they faced a critical challenge in providing and maintaining a stable voltage supply to power the purification system effectively.
To ensure optimal performance, the air purification system required a closed-loop control mechanism managed by a Microcontroller Unit (MCU). The optimum voltage could be achieved and maintained by PWM signals generated using the ECU.
In a nutshell, the requirement was to build an air purification ECU with the required hardware and software. Since the system was intended to be designed for automotive use-cases, ASPICE Level 2 compliance was required.
Embitel’s Solution:
Embitel’s expert engineering team collaborated closely with the customer to develop a comprehensive and efficient solution for their cabin air purification system.
The solution involved the development and testing of hardware components and various software layers and applications based on customer specifications. Our ASPICE compliance team was taken on-board for continuous assessment and audit as per ASPICE L2.
After the projects milestones were established, the hardware and software teams began to jointly develop the air purification ECU.
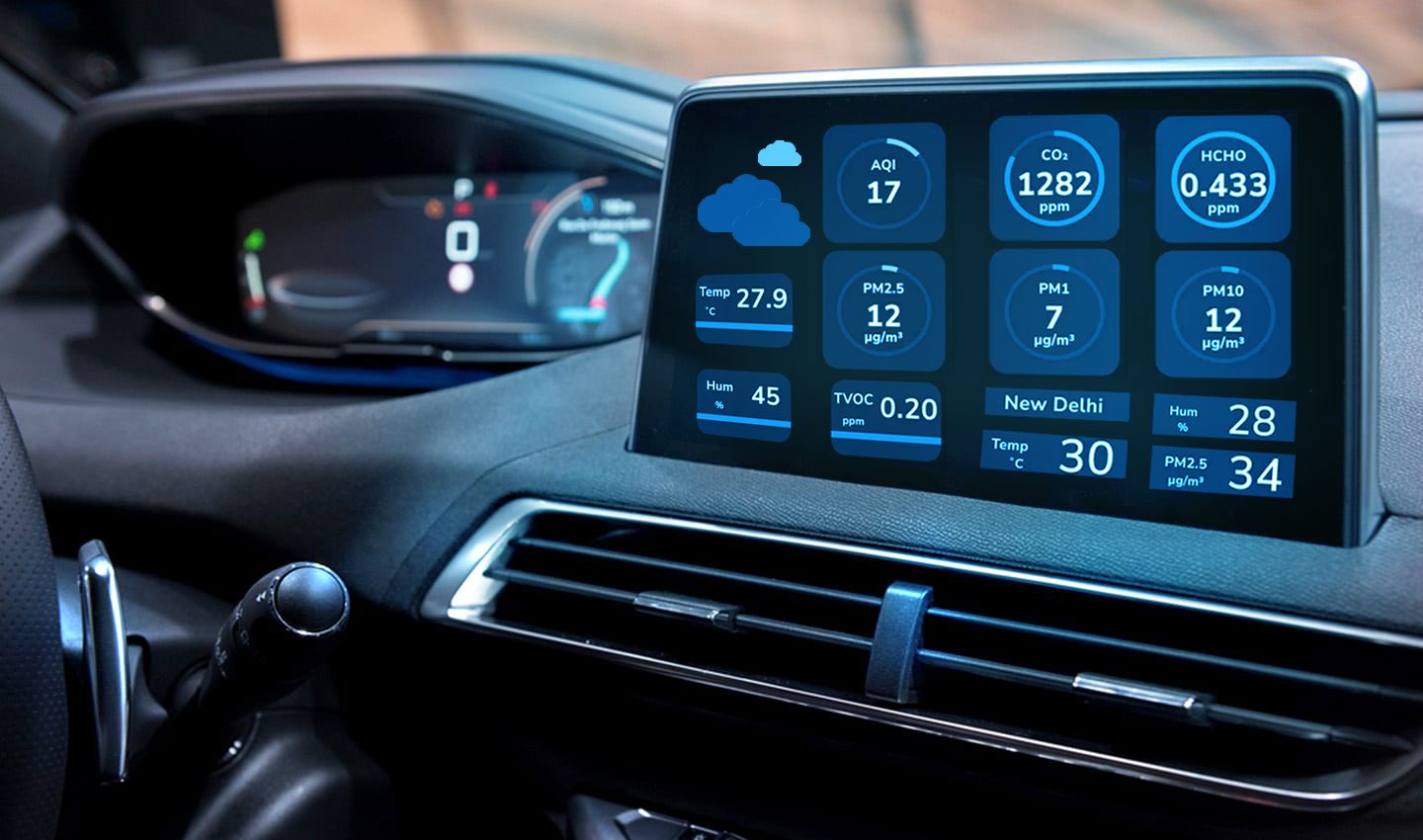
A Snapshot of ASPICE Level 2 Compliant Hardware Development and Testing
Embitel’s hardware development for the Automotive Cabin Air Purification System project followed ASPICE L2 guidelines, ensuring a systematic and robust approach to deliver high-quality hardware components. The ECU was responsible for processing data from various sensors, controlling the purification process, and interacting with the software components.
The hardware development process included the following key stages:
- Hardware Schematic Design for ECU
- Simulation Tests
- Board Bring Up and Module Testing
A detailed hardware schematic was meticulously designed, considering the system requirements, component specifications, and ASPICE L2 guidelines
Prior to physical board fabrication, the hardware team conducted extensive simulation tests using advanced simulation tools.
In the board bring-up stage, the newly assembled ECU boards were powered up and tested for basic functionality and initial communication with other components. Module testing involved rigorous testing of the ECU’s individual functionalities and interfaces to verify their performance against specifications.
In addition, Embitel conducted EMC/EMI testing to ensure that the ECU complied with relevant electromagnetic standards and did not interfere with other electronic systems in the vehicle.
Important Hardware Modules in the ECU
DC-DC converter: DC-DC converter was required for buck/boost. A high-voltage control was needed for air purification system to operate, and a low voltage DC-DC converter supplied lower voltage to the MCU.
Microcontroller: An automotive grade MCU was used to execute the algorithm for generating optimized PWM signal.
A Snapshot of Software Development of Air Purification ECU
The software part of the air purification ECU comprised of various layers including the application as well as the base software layer.
While traversing the requirement specifications, our automotive team realized that the application layer is quite complicated. And thus, model-based development approach was taken.
For base software, the team went with manual coding.
- Model-based Development of Application Software Layer: The application layer encompassed a couple of applications developed based on customer specifications, including:
- System Manager: Responsible for managing and coordinating various functionalities within the air purification system.
- Application for Air Purification: Utilized pulse-width modulation (PWM) to generate an optimum voltage for air ionization, ensuring efficient air purification.
- Low-level drivers: Comprised of watchdog timer (WDT), microcontroller driver, SPI, PWM, Code Flash, LIN slave drivers, etc.
- Safety and service layer: Stack overflow driver, CPU overload detection algorithms, self-diagnostics, etc.
- Development of COM layer: LIN based communication through our ready-to-integrate LIN protocol stack (LIN interface, Lin NM layer and LIN Transport layer).
- UDS based Diagnostics Layer Implementation: UDS server stack implemented as per ISO 14229. UDS stack was configured as per the specifications and integrated with the ECU. UDS based bootloader was also implemented.
MISRA C 2012 compliance was achieved using tools like Polyspace.
We also performed unit, integration, and functional testing for the modules.
Project Compliance with ASPICE L2
Our development of the Automotive Cabin Air Purification System adhered to the rigorous ASPICE Level 2 requirements.
Embitel’s Impact:
Embitel’s expertise in developing new-age automotive solutions, particularly ASPICE-compliant solutions for cabin air quality improvement, had a profound impact on the success of the project.
Our library of reusable modules and a robust base software framework played a pivotal role in accelerating the development process.
Our ready-to-deploy LIN and UDS stacks further streamlined the development process by at least 6 months.
Tools and Techniques:
- NXP IDE – Code editing, compiling and debugging
- Tessy – Unit and Integration testing
- Polyspace – Static code analysis
- SIMULINK – Model based development of application software